Magnehelic Gauge has become a game-changer in the field of pressure measurement. Known for its precision and reliability, it is an innovative tool designed to measure low differential pressures seamlessly. Specifically tailored for industries such as HVAC (Heating, Ventilation, and Air Conditioning), manufacturing, and other engineering applications, the Magnehelic Gauge is renowned for delivering accurate results in environments where precision is critical.
But what truly sets it apart? Not only does it ensure error-free readings, but its user-friendly design and robust construction make it a must-have for professionals. Whether you’re an engineer, HVAC technician, or part of the manufacturing sector, the Magnehelic Gauge simplifies your task by providing a clear and instantaneous visual pressure reading.
Now, let’s explore its applications and discuss how it has revolutionized pressure measurement across industries, adding value beyond just numbers.
Understanding the Magnehelic Gauge
How Does the Magnehelic Gauge Work?
At the heart of its operation, the Magnehelic Gauge measures differential pressure—the difference between two pressure points—through a sensitive diaphragm mechanism. This diaphragm is deflected proportionally to the pressure differential, and the movement is displayed on a calibrated dial.
The transition of pressure readings into an intuitive visual format ensures ease of operation, even for newcomers to the tool. Users quickly grasp the nuanced details of air or gas pressure levels in real-time without needing elaborate calculation or interpretation.
Advantages of the Magnehelic Gauge
When compared to traditional pressure measurement devices, the Magnehelic Gauge stands apart with numerous benefits such as:
- High Durability: Built to withstand harsh conditions, the gauge performs consistently in challenging environments.
- Instant and Reliable Readings: Time-sensitive industries value its ability to provide real-time, accurate measurements.
- Versatility: It’s widely adaptable for liquid, gas, or air pressure measurements.
- Low Maintenance Requirements: Unlike other devices, it demands minimal upkeep to deliver accurate results.
Disadvantages of the Magnehelic Gauge
Limited Range of Measurement
While the Magnehelic Gauge excels at measuring low-pressure differentials, it is less effective in situations that require the measurement of extremely high pressures, which may require alternative devices.
Vulnerability to Damage
Despite its durability, the gauge’s internal components can be sensitive to physical impacts or exposure to certain corrosive substances, potentially leading to damage or reduced accuracy over time.
Calibration Needs
For long-term precision, the gauge requires periodic calibration. This can be an inconvenience for users who need consistently reliable readings without spending additional time on maintenance.
Cost Considerations
Compared to some simpler pressure measuring devices, the Magnehelic Gauge can be relatively expensive, presenting a budgetary constraint for smaller operations or projects.
Limited Compatibility with Certain Applications
The gauge may not be suitable for all industrial settings, particularly those requiring highly specialized or unconventional pressure measurement solutions.
Real-world Applications
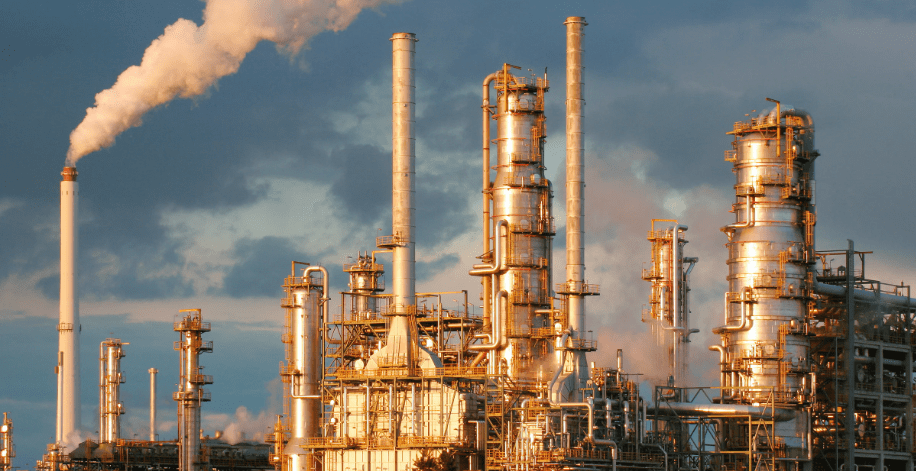
Industries around the world have embraced the Magnehelic Gauge for its precision and functionality.
- HVAC Systems: Professionals use it for ensuring appropriate airflow and monitoring filters in ventilation systems.
- Pharmaceutical Manufacturing: Compliance with cleanroom standards often requires monitoring pressure differentials, making the gauge indispensable.
- Oil Refineries: It helps in detecting any pressure anomalies to prevent operational hazards.
The Magnehelic Gauge ensures efficient and safe operations regardless of its application, proving its indispensability time and again.
Evolution of Pressure Measurement
The Origin of Pressure Measurement Tools
Pressure measurement dates back hundreds of years, with rudimentary tools like barometers paving the way. However, technological advancements saw the advent of more sophisticated instruments such as manometers and Bourdon tube gauges.
While these were reliable during their time, industries faced growing demands for precision, durability, and versatility—needs that traditional tools struggled to fulfill entirely.
The Arrival of Magnehelic Gauges
Since their inception, Magnehelic Gauges have addressed several limitations of traditional instruments. By offering improved accuracy, user-friendly interfaces, and compatibility with modern industries, these gauges set a new standard, becoming a benchmark for pressure measurement excellence.
What’s Next for Magnehelic Technology?
Technological innovation hints at an exciting future for Magnehelic Gauges, incorporating wireless connectivity, IoT integration, and advanced analytics. These additions promise to add further value, bridging the gap between on-site operations and digital monitoring platforms.
Features and Variations
Key Features of the Magnehelic Gauge
Here’s what makes it a standout tool in its category:
- Wide Measurement Range: Adaptable to different pressures across industries.
- Clear Display: Easy-to-read dials ensure quick interpretation of results.
- Robust Construction: Designed for durability under extreme conditions.
- Compact Design: Enables installation in spaces with minimal clearance.
Variations to Suit Specific Needs
Different industries demand varied specifications, and the Magnehelic Gauge responds with customizable options. From dust-resistant and waterproof variants to models offering extended-range pressure measurement, there is a gauge for every requirement.
Installation and Maintenance
Proper Installation Practices
The efficiency of a Magnehelic Gauge depends heavily on its installation. Below are some steps for the best results:
- Choose Correct Mounting Locations: Ensure an environment devoid of extreme vibrations and temperature variations.
- Follow Calibration Protocols: Test for accuracy during installation by comparing readings with calibrated standards.
- Secure Connections: Avoid pressure leaks by ensuring all pipelines are tightly secured.
Maintenance Tips for Extended Lifespan
Like any precision instrument, a Magnehelic Gauge requires regular maintenance to function optimally.
- Keep it Clean: Dust and debris can hinder the dial’s motion, so periodic cleaning is necessary.
- Check for Wear and Tear: Replace damaged diaphragms or gaskets to maintain accuracy.
- Re-calibrate Periodically: This ensures consistent measurement over time.
Comparisons with Other Devices
Magnehelic Gauge vs. Digital Pressure Gauges
1. Accuracy
- Magnehelic Gauges: These gauges offer reliable and consistent readings, suitable for many industrial and commercial applications. However, their accuracy can slightly decrease if not calibrated regularly.
- Digital Pressure Gauges: Digital gauges often provide higher precision and can display readings with greater granularity, making them ideal for applications requiring exact measurements.
2. Durability
- Magnehelic Gauges: Designed with durable materials, they perform well in harsh conditions, making them a choice for rugged environments.
- Digital Pressure Gauges: While robust, digital gauges can be more susceptible to damage from extreme conditions, such as water or physical impacts, without additional protection.
3. Ease of Use
- Magnehelic Gauges: Their straightforward, analog display makes them easy to operate without requiring technical expertise.
- Digital Pressure Gauges: These often feature digital interfaces that may include additional functionalities but can be more complex to use for individuals unfamiliar with the technology.
4. Maintenance and Longevity
- Magnehelic Gauges: Require minimal maintenance and provide a long service life, as they don’t rely on electronic components.
- Digital Pressure Gauges: While generally low-maintenance, their electronic parts may need periodic checks or replacements, which could impact their lifespan.
5. Cost
- Magnehelic Gauges: Offer a cost-effective solution, particularly for applications that do not need the advanced features of digital models.
- Digital Pressure Gauges: Typically more expensive upfront due to their additional features and advanced capabilities.
6. Applications
- Magnehelic Gauges: Ideal for general pressure monitoring in HVAC systems, cleanrooms, and industrial settings where precise digital outputs are not essential.
- Digital Pressure Gauges: Suitable for high-precision tasks, laboratory settings, and industries where digital data integration is necessary for system monitoring.
7. Data Integration
- Magnehelic Gauges: Operate as standalone devices without digital integration.
- Digital Pressure Gauges: Can often connect to other systems through interfaces such as Bluetooth, USB, or wireless connectivity, enabling advanced monitoring and data recording.
Summary
While both Magnehelic and digital pressure gauges have their advantages, the choice between them ultimately depends on the needs of your application, budget, and the environmental conditions of use.
Future Trends and Innovations
Advancements in Pressure Measurement Technology
The field of pressure measurement is evolving rapidly, with innovations aimed at improving accuracy, reliability, and ease of use. Emerging technologies, such as wireless connectivity and IoT-enabled devices, are changing how data is collected and analyzed.
Integration with Smart Systems
Future trends point toward Magnehelic Gauges being integrated into smart systems. By combining mechanical reliability with digital enhancements, these gauges may soon offer hybrid models capable of synchronous monitoring in automated environments.
Sustainability and Eco-Friendly Designs
With increased focus on sustainability, manufacturers are exploring eco-friendly materials and designs. This trend ensures that future devices align with global environmental goals while maintaining performance standards.
Miniaturization and Portability
Miniaturization is another area of innovation, leading to smaller, more portable pressure gauges. These compact models will provide flexibility for use in tighter spaces and remote locations without compromising functionality.
Enhanced Durability for Extreme Environments
Future iterations of Magnehelic Gauges may include features specifically designed for extreme environments, such as higher tolerance to temperature fluctuations and improved resistance to corrosive elements.
Must Read : Lloyd Jones Net Worth 2024: Trader, Footballer & Entrepreneur
Environmental and Economic Benefits
Reduced Energy Consumption
Advancements in Magnehelic Gauges could lead to better energy efficiency by providing more precise measurements, ultimately optimizing system performance. This would result in lower energy usage across industries, helping to reduce carbon footprints and contribute positively to environmental sustainability.
Minimized Waste
Improved accuracy in monitoring and controlling air pressure can reduce waste in a variety of processes, from manufacturing to HVAC systems. By ensuring operations run optimally, less material is wasted, directly benefiting both the environment and organizational costs.
Cost Savings through Longevity
Enhanced durability and reliability in future Magnehelic Gauges would decrease the frequency of replacements and repairs. This not only reduces operational costs for businesses but also lowers the environmental impact by reducing the demand for manufacturing new units and disposing of old ones.
Sustainable Resource Use
New materials and manufacturing techniques could prioritize sustainability, making Magnehelic Gauges more environmentally friendly. The use of recyclable components or renewable resources aligns with global efforts to promote sustainable industry practices.
Impact on Industry
Improved Efficiency
The adoption of advanced Magnehelic Gauges has significantly improved operational efficiency across various industries. These gauges allow for precise measurement of differential pressure, enabling more accurate system monitoring and adjustments. This leads to optimized performance, reduced energy consumption, and minimized downtime.
Enhanced Safety Standards
Industries that rely on pressure systems, such as HVAC, pharmaceuticals, and manufacturing, benefit from the enhanced safety provided by these gauges. Accurate pressure monitoring helps detect potential issues early, mitigating risks such as equipment failure or hazardous leaks, ensuring both worker safety and compliance with regulatory standards.
Cost-Effective Operations
By integrating durable and reliable Magnehelic Gauges, industries experience reduced maintenance and repair costs. Their longevity and ease of calibration lower the financial burden on businesses, making them a cost-effective solution for long-term operations.
Positive Environmental Impact
Magnehelic Gauges, designed with sustainability and precision in mind, contribute to the reduction of energy waste and resource overuse. Industries implementing these devices align with global environmental goals, bolstering their commitment to sustainable practices while maintaining operational effectiveness.
Join the Revolution in Pressure Measurement
- Enhanced Durability: Experience gauges built to last, designed to withstand demanding environments and reduce replacement needs.
- Eco-Friendly Designs: Benefit from sustainable innovations using recyclable materials and renewable resources.
- Accurate and Reliable Measurement: Rely on cutting-edge technology to deliver consistently precise pressure readings.
- Cost Efficiency: Minimize operational costs with durable, low-maintenance solutions.
- Future-Forward Innovations: Stay ahead with gauges tailored for modern industrial and environmental requirements.
Overview of Magnehelic Gauges
What are Magnehelic Gauges?
Magnehelic Gauges are precision instruments designed to measure differential pressure with exceptional accuracy and reliability. These gauges are commonly used to monitor and maintain pressure in various systems, ensuring optimal performance and compliance with industry standards.
Key Features of Magnehelic Gauges
- Very Precise: The devices deliver accurate outputs and thus, are appropriate for vital uses.
- Durability: Constructed with robust materials to withstand harsh environments and long-term use.
- Easy Installation: Designed for quick and hassle-free mounting in a wide range of systems.
- Wide Measurement Range: Capable of monitoring low-pressure differentials to more extreme ranges with the same effectiveness.
- Low Maintenance: Built for consistent performance with minimal upkeep required.
Why Choose Magnehelic Gauges?
Reliability and Performance
Magnehelic gauges are renowned for their reliability and consistent performance. They are engineered to deliver accurate readings even under challenging conditions, ensuring that systems operate efficiently and safely.
Versatility in Applications
These gauges are suitable for a diverse range of industries, including HVAC, pharmaceuticals, cleanrooms, and manufacturing. Their ability to adapt to different systems and environments makes them a versatile choice for professionals.
Cost-Effectiveness
With robust construction and low maintenance requirements, Magnehelic gauges reduce the long-term cost of ownership. Their dependable performance minimizes the need for frequent replacements or repairs.
User-Friendly Design
The intuitive design of Magnehelic gauges ensures ease of use, allowing operators to read and interpret results quickly. The clear, marked display makes monitoring simple and efficient, saving time and effort.
Proven Track Record
Backed by years of successful application across industries, Magnehelic gauges have earned trust and respect for their quality and efficiency. Choosing these gauges means investing in a product with a proven history of excellence.
Key Takeaways about Magnehelic Gauges
- Reliability: Magnehelic gauges provide accurate and consistent results, ensuring reliable performance across various applications.
- Durability: Constructed with robust materials, these gauges are built to withstand demanding environments and offer long-lasting service.
- Ease of Use: The clear and intuitive design allows for quick and simple interpretation of measurements, reducing operational complexity.
- Cost-Effective: With low maintenance needs and dependable performance, Magnehelic gauges offer excellent value over time.
- Proven Performance: Trusted by industries for years, these gauges uphold a strong reputation for quality and efficiency.
- Versatility: Suitable for monitoring and maintaining differential pressure in a wide range of applications, making them a versatile tool.
Conclusion
Magnehelic Gauges represent the pinnacle of precision, sustainability, and innovation in pressure measurement technology. By integrating these advanced gauges into your operations, you not only enhance efficiency and reliability but also demonstrate a commitment to eco-conscious practices. Join countless industries already benefiting from the seamless blend of performance and sustainability. It’s time to elevate your processes with them and take a step toward a more efficient and environmentally responsible future.
Frequently Asked Questions (FAQs)
- What is a Magnehelic Gauge?
It is a precision instrument used to measure differential pressure in various industrial and environmental applications. It is known for its accuracy, reliability, and eco-friendly design.
- How does a Magnehelic Gauge work?
It measures the difference in pressure between two points by utilizing a diaphragm or other sensing mechanism that displaces the pointer on the gauge face.
- What industries benefit from using Magnehelic Gauges?
Industries such as HVAC, manufacturing, healthcare, and environmental monitoring frequently use them to ensure optimal system performance and safety.
- Are Magnehelic Gauges environmentally friendly?
Yes, these gauges are designed with sustainable materials and processes, making them a choice aligned with eco-conscious business practices.
- Do Magnehelic Gauges require regular maintenance?
These are known for their durability and low maintenance, although occasional cleaning and calibration may be necessary for optimal performance.
- Can I install a Magnehelic Gauge myself?
Many of it come with straightforward installation instructions, but it is advisable to consult a professional for complex systems.
- What pressure ranges do Magnehelic Gauges support?
It support a wide range of differential pressures, making them suitable for both low and high-pressure applications.
- Are Magnehelic Gauges compatible with modern systems?
Yes, these gauges are designed to meet the requirements of modern industrial and environmental systems, ensuring seamless integration.
- How can I ensure accurate readings from my Magnehelic Gauge?
To ensure accuracy, regularly inspect the gauge for dirt or damage and perform calibrations as recommended by the manufacturer.
- Where can I purchase Magnehelic Gauges?
It can be purchased from authorized distributors, reputable online stores, or directly from manufacturers specializing in industrial measuring equipment.
Read More : Syna World: Transforming Dreams into Reality